Lightwire has a continuous and well-resourced focused on the health and safety of our people, partners, and customers. In this article, we will get into the details of how we make sure our people get home safe.
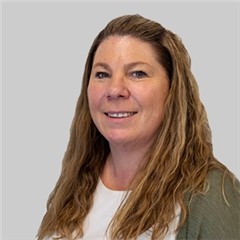
The foundation
Lightwire demonstrates to our partners and employees that we are serious about their Health and Safety through having a team member solely focused on Health and Safety, enforcing one of our core values – CARE. CARE is the company value that we, as a company are focused on the best possible outcomes for our customers, community, and team, which can only happen when everyone is safe and sound.
Commitment from Lightwire’s senior leadership team (SLT) to a transparent process has laid a foundation built on trust and transparency Employees speak up and are listened to, nothing is buried in processes, employee engagement is high and directed into quality discussions that allow employees room to make the right decisions.
Sharing is caring
Lightwire does not measure Health and Safety success on the absence of incidents. Instead, we encourage our team to regularly share near misses or lessons via a dedicated health and safety channel in Microsoft Teams. This generates open discussion from which ideas for correctional action or preemptive improvement to processes are gained.
Learn from near misses
One real near-miss posted was due to an employee accidentally leaving their canopy “wings” up. This could have resulted in gear falling out hitting other vehicles on the road, or damage to the Lightwire vehicle itself.
As a result of sharing this near miss, all ute canopies have been fitted with a door alarm. Now, when the driver starts the ute, he/she will be alerted immediately if wings are still up…
Not your standard training
While there is certainly a place for a standard first aid course with a refresher every two years, we established that one of our key critical risks was on-road driving. This was due to the amount of time Lightwire’s Field Technicians spend on the road meaning that they are statistically more likely to come across or be involved in, a serious road accident.
We engaged Oceania Medical to build a customised first aid and serious trauma training program focused around all of our main critical risks, as well as the management of injuries that Lightwire’s Field Technicians could potentially be confronted with. The training is now delivered in a comparable environment in less-than-ideal conditions to enable the team to experience real obstacles they could be faced with.
This experience led us to look at our first aid kits objectively and stock these with items more useful in the sort of scenarios we are likely to face, a window breaker for car accidents for example. Having the right tools for the job is paramount, and listening to what Field Technicians require in the field has allowed them us to think outside the square and develop smart safe solutions such as the custom-made rack to transport ladders on our off-road vehicle (or in the case of emergency this doubles as a stretcher).
With a culture of caring for each other, Lightwire employees are comfortable reporting incidents and sharing their experiences with each other with the aim of creating a better, healthier, and safer work environment for everyone.
Lightwire’s H&S team is ensuring that effort is directed proportionate to risk levels, and while a greater percentage of our time and effort is directed to the field teams critical risks, health and safety is also incorporated into our office environment with customised workshops built for defibrillator training, work- station set up and more.
It was recently noted in an audit assessment, with a score of 95% compliance, completed for Crown Infrastructure Partners Ltd, that;
How about health & safety in the office?
The most recent workshop for Lightwire’s office workers was built around workplace ergonomics or in normal speak, how you organise your workstation to reduce neck and back injuries, as well as stress. Everyone knows how to operate a computer, but when the occupational therapist inspected all the desks it became clear that very few had set up their workstations correctly.
The occupational therapist worked together with office personnel to set up their workstations as well as equip them with tools that help reduce office-work related muscle strain, muscle imbalances, and fatigue.
In summary
An environment where everyone is involved in the investigation process, freely contributes, and offers information creates a safer and healthier work environment. Some key concepts that helped us get our Health and Safety to where we are today are;
- Health & Safety programs only work if employees are trusted, engaged, and supported
- Training only helps when it closely mimics real-life conditions and scenarios.
- Equip team members with the items and tools that are practical for the situations they could face and train them on how to use each item.
- Health & Safety is never done, there’s always room for improvement.